Choosing the right Wheel Equipment for your Company
Just a quick guide from our friends over at Gibson Abrasive Equipment Co. on how to choose the right wheel blast equipment to meet your needs. We are a distributor for Gibson and will help you with your purchase every step of the way. Click through for more!
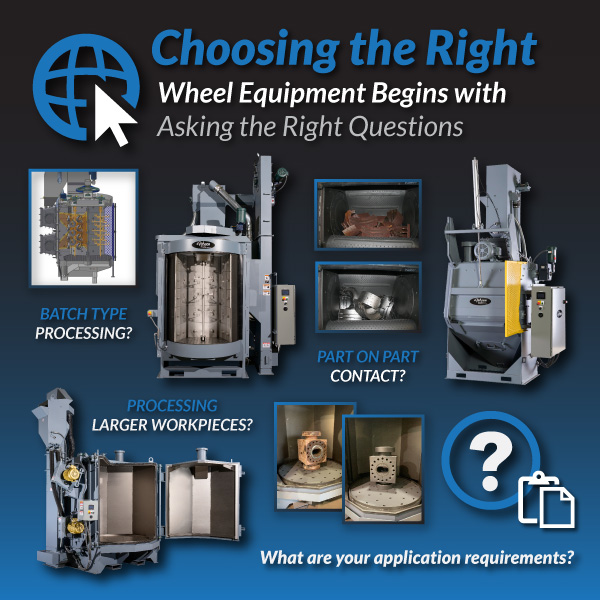
Cheektowaga, NY – Release: March 22, 2021
Just a quick guide from our friends over at Gibson Abrasive Equipment Co. on how to choose the right wheel blast equipment to meet your needs. We are a distributor for Gibson and will help you with your purchase every step of the way, contact us today at 716-948-4002!
1. Does your application require shot peening, cleaning, deburring, deflashing, or just surface preparation?
Brief definitions:
- Peening – To stress relieve or harden the surface of a part.
- Cleaning – Remove rust, scale or just a generally even look.
- Deflashing – Removing flash under 1″ in size.
- Deburr – To roll the edge of a part, tame down a sharp edge, remove general burs.
- Surface preparation – Generally known as preparation for rubber bonding, adhesion, paint, some surfaces require particular RA factors.
- RA Factor – A microscopic or magnifying glass view will reveal a crater like surface with shot & a saw tooth surface with grits. This surface roughness can be increased by wheel velocity and/or media size.
Other questions to consider:
- Is it important to blast the inner diameter or just the outside diameter of the part, or both?
- What is the smallest part size?
- Is it sharp or pointed?
- What is the largest part?
- How is the part shaped?
- What is the production requirement that we need to keep up with? Volume? Number of Shifts?
- Do you want a batch type or an inline/flow through type blaster?
- Do you want to pile up parts and then run them or are you looking for a lean manufacturing set up?
2. Inline or Flow Through Type?
Inline or flow through type blasters such as wire mesh belt blasters, are typically more expensive, require a trained technical service person for maintenance, and create dependence on one unit if multiple machines are not purchased. Whereas batch type blasters are less expensive, easier to work on, and are great for lean manufacturing and batch cleaning.
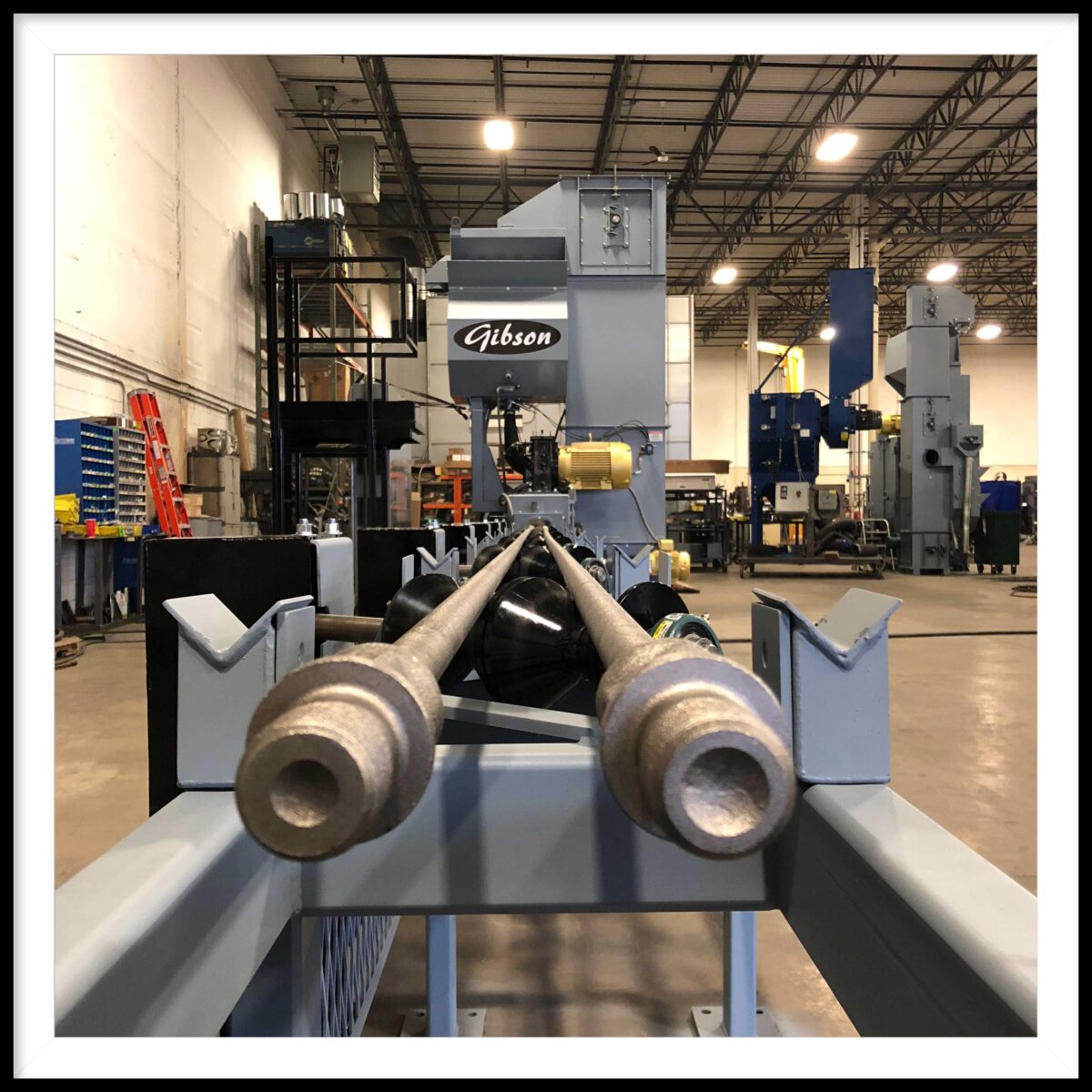
Questions that Gibson might ask when fitting you into the right flow through blaster:
- Can it be hung on a fixture? If it can hang does it need to spin once it’s in the blast area or can it just move through the unit without rotating? Will it stay on the tree or fixture during the blast cycle?
- Can I roll it through on a roll conveyor?
- Can I lay the part on a mesh belt? Do I have any blinding concerns? The mesh belt leaves a shadow due to mesh belt blocking the media from hitting the part directly.
Batch Type Blasters
Batch type blasters are an inexpensive way to get into blasting. They are great for lean manufacturing applications and are easy to work on once in the field. Gibson builds three main types of them, tumble blast, spinner hanger blast, and table blasters.
What is a Tumble Blaster?
It is similar to a rock tumbler or cement mixer except instead of being completely enclosed in a round barrel it has a rubber mill belt or conveyor that it continuously rolling in the shape of a J. Hence the name J belt. There are one or two blast wheels mounted on top throwing media down at the parts that are tumbling due to the upward movement.
The belts have holes in many sizes and patterns. Typically, they have cleats which create better tumbling action. The rubber mill conveyor belts come in standard and cross rigid materials. The reclamation system recovers the media using a bucket elevator recovery system that are sometimes assisted by an auger or two. They have an air wash separator to remove the fines and also many other options.
Tumble Blast Advantages:
- No manual flipping or rotating
- All sides will be blasted if they tumble properly.
- Used in applications where batches of parts can tumble on top of each other without causing damage to the parts.
- Typically used in automotive remanufacturing, heat treat facilities, and small spring peening applications.
- Can run large batches of smaller parts all together.
Tumble Blast Disadvantages:
- Some customers blasting parts do not want the parts tumbling onto each other.
- The parts can’t be sensitive to part on part contact.
- Clustering
- Not continuous so you have to wait
- Parts have to be less than 200-degrees due to the rubber mill belt. A 400-degree belt is available but the intention is that the part is moving and not lying on the belt when it’s that high of a temperature.
What is a Spinner Hanger?
A means of blasting parts while hanging them on a fixture or tree. The fixture with parts on it will rotate while being blasted with one or more blast wheels that are typically mounted on the back or side of the cabinet. Dual chamber spinner hangers allow you to add/remove parts while the other side is blasting making it “as efficient as possible”. They also allow the chamber to index during blasting.
Hangers allow you to buy oscillating blast wheels or some actually move the parts/fixture to different positions during the blast cycle. Single and Y-track monorails are offered as well as hanger table combo models.
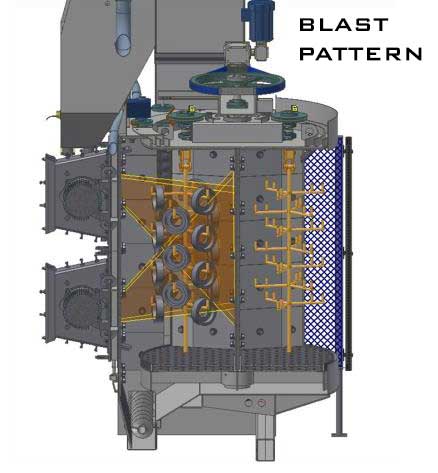
Specific Questions when deciding on what type of spinner hang that you need:
- Do you need to load and unload while the other side is blasting? A dual chamber spinner hanger is the faster and most productive route to go between the two main options.
- Is it fine if I push the fixture with parts on it into the cabinet, close the door and wait five minutes or so? In/out box type is the route to go here.
- How heavy are the parts? If they are too heavy, you might go with the in/out box route.
- Will the part swing or rotate when the blast media hits it? If you have concerns with parts swinging, then an in/out box might be the way to go.
What is a Table Blaster?
It’s a blast cabinet with typically one or two blast wheels aimed at an odd shaped or heavy part that is laying on a round table. The table rotates like a microwave turntable typically in a CCW direction when standing on it looking down. The reclamation system recovers the media using a bucket elevator recovery system that are sometimes assisted by an auger or two. They have an air wash separator to remove the fines.
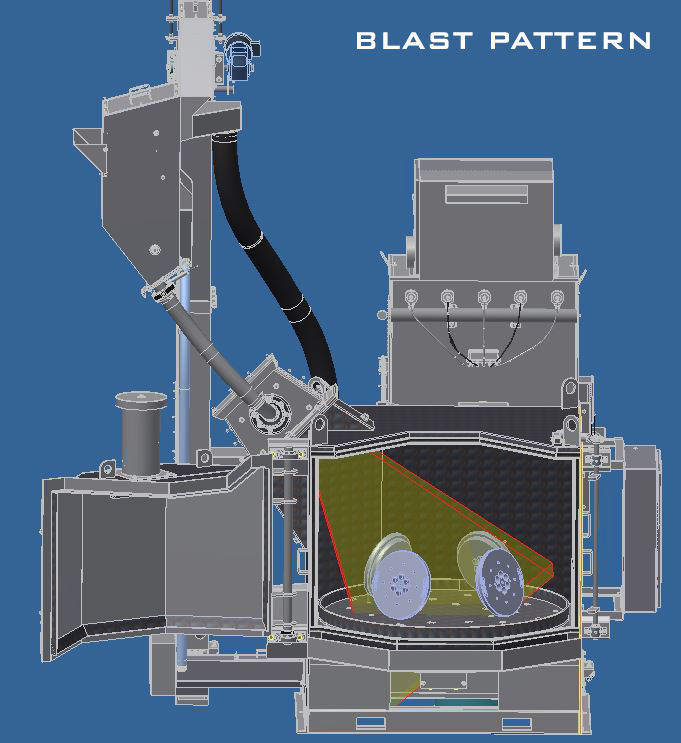
Table Blast Advantages:
- Mostly used for odd shaped or heavy parts that can’t easily be hung or tumbled.
- It’s typically a more economical solution where the parts could be hung but the customer can’t a spinner hanger. Typically, not for small parts.
- Better for lower volume parts.
- Somewhat indestructible compared to a rubber belt or spinner hanger (robust).
- Typically used in the oil & gas industry.
- Multipurpose – You can lay parts on the table or hang them on a fixture that is mounted on the table.
- Allows for larger parts and smaller parts in the same machine.
Table Blast Disadvantages:
- Some (not all) applications require you to move the parts during the cycle to ensure even coverage.
- The parts may need to be flipping or rotated due to blinding.
- Speed
Tags: Gibson, Wheel Blast Buffalo