High Energy Finishing
The Hammond Roto-Finish vibratory finishing machines are a new development in vibratory mass finishing.
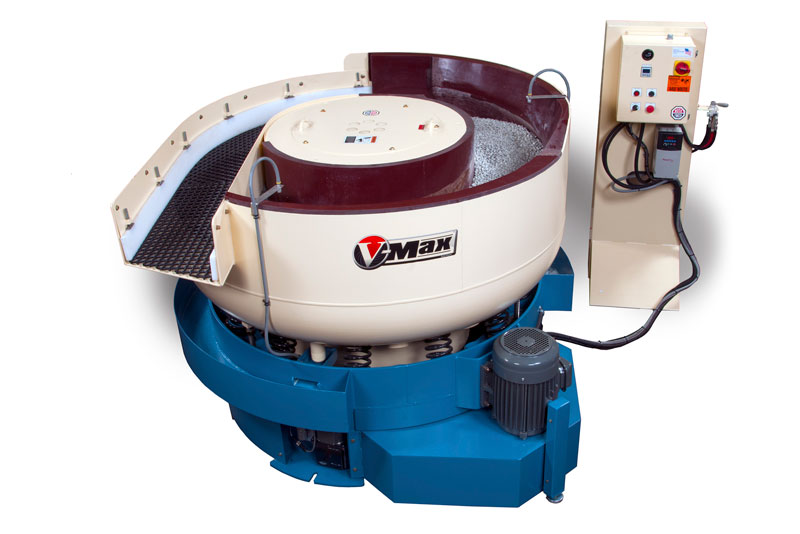
V-MAX®
The Hammond Roto-Finish V-Max® series vibratory finishing machines are a new development in vibratory mass finishing.
The V-Max® machine is based on the design of the “HR” machines built by Hammond Roto-Finish. The main component of the HR bowl is the certified pressure vessel that forms the bottom of the bowl, with the completed weldment the bowl structure is a “dome”. The weldment design and vibratory drive design allow the V-Max® bowl to operate at speeds no other vibratory bowl can match.
Up to 50% Cycle Time Reduction over Conventional Vibratory Machines!
The design of the bowl and drive in conventional machines create “bounce” within the media that translates into air time between the media and part.
In the redesigned V-Max®, the force of the machine is more directly applied to the media, putting more energy into the roll of the media. The roll, visually apparent while the machine is running, creates a dramatically increased media-on-part contact time. This is demonstrated in the amplitude difference of the machines.
The increased contact time, along with the increased force of the higher RPM, is the cause of the reduced cycle time.
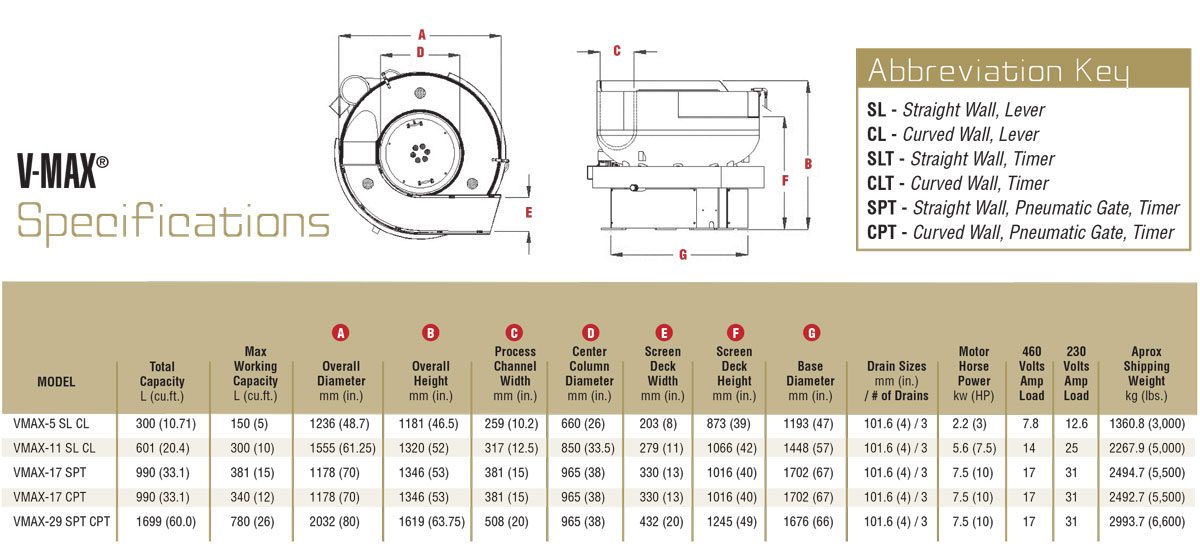
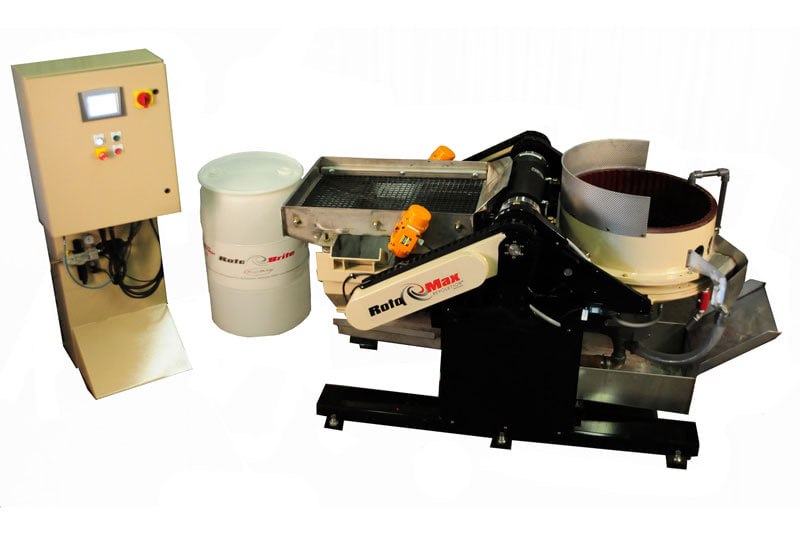
ROTO-MAX® REVOLUTION
The Roto-Max® Revolution is a new patented “all-in-one” machine from Hammond Roto-Finish. The Revolution features the RM-2 or RM-6 centrifugal disc section integrated into a machine that has one main moving pivot point which, depending on which feature is activated, will move the process bowl to empty the media and part mixture onto the built-in separator. This built-in separator is also the return media hopper, so the media is automatically reloaded into the process chamber to start the operation over again.
The Roto-Max® Revolution is compact and can be easily expanded to accept added features for material handling, or secondary processing steps.
All Standard Units Include:
- Semi-Automatic Control Panel (Free standing)
- Non-Electric Compound System
- 230/460V, 3 PH, 60 HZ
- Smooth or Ribbed Polyurethane Wall
- Patented Up-Flow®System
- Variable Speed
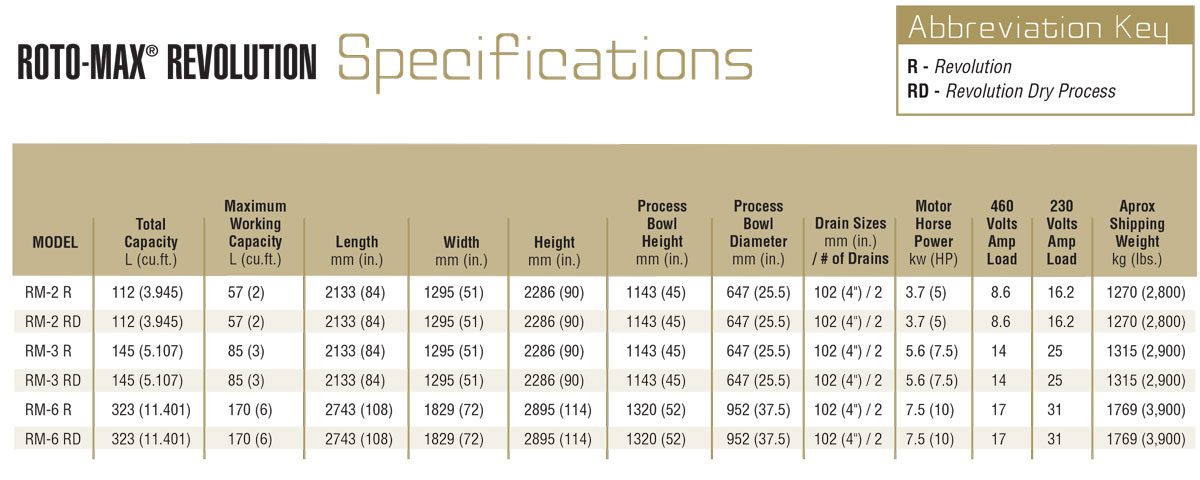
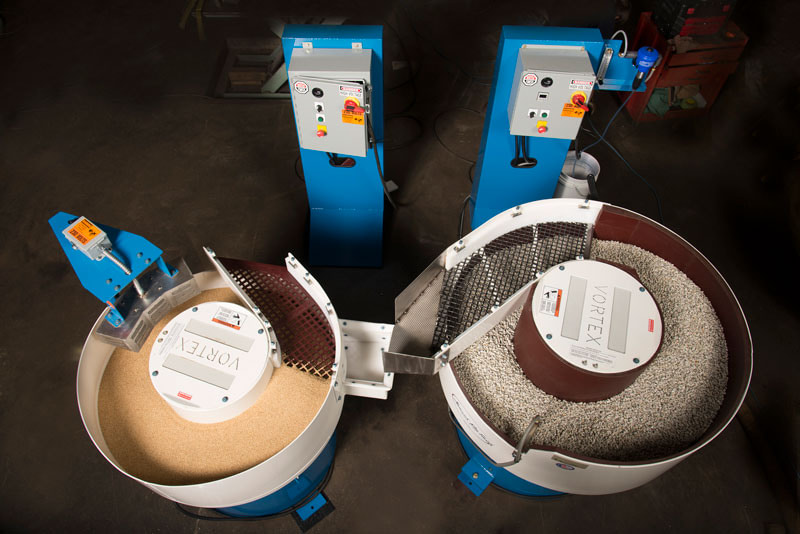
GEMINI® VORTEX
Gemini® Vortex machines feature an integral drive. This drive offers lower maintenance, higher frequency and a faster process time.
- Medium frequency machines (1,800 RPM)
- Proven Weldment Design
- Faster Material Removal than Conventional Vibratory Machines
- Metric Fasteners for World Market
- Included with Machine: Compound System, Two Screens, Four Drain Inserts
- 2 Year Drive Warranty
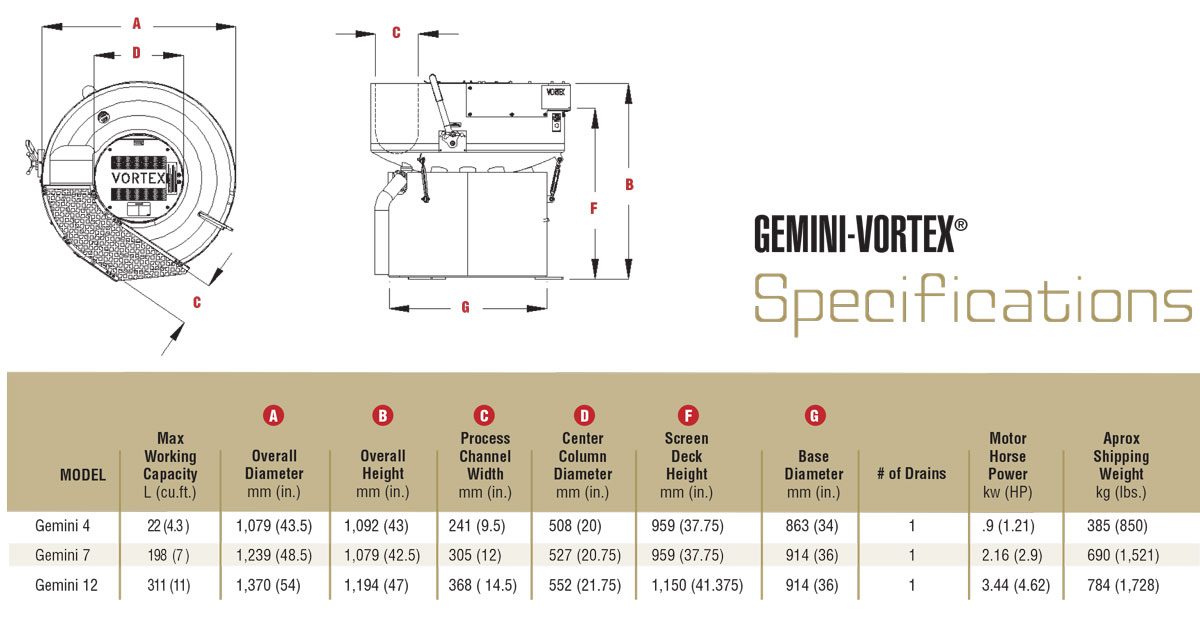
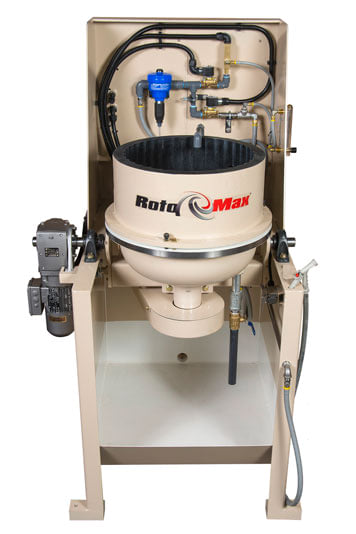
ROTO-MAX®
The Roto-Max® has a unique compound delivery system in the centrifugal disc market. The patented process is called Up Flow®. The name is derived from the compound being added to the bowl from under the media, and the resulting waste then exiting through a drain near the top of the media.
This Up Flow® technology, along with the adjustable seal gap height, greatly lengthen the life of the seal gap over other centrifugal disc machines. The greatest wear to the urethane lining are the particulates that come off the parts and media as it wears. With down flow compound, the particulates are sent through the lining.
Up Flow® technology significantly reduces the wear on the urethane, so can expect to have more ‘up time’ a with Roto-Max centrifugal disc than other centrifugal disc machines.
- Cycle Times up to 15 Times Faster than Vibratory Finishing.
- Improves Surfaces: Deburrs, Descales, Deflashes and Burnishes.
- Advanced Seal Design Prevents Intrusion of Smaller Parts and Media, thus Prolonging Tub and Rotor Life.
- Processes all Types of Material –Metal, ceramic, plastic and rubber.
- Wider Range of Surface Finishes are Attainable with a Given Media.
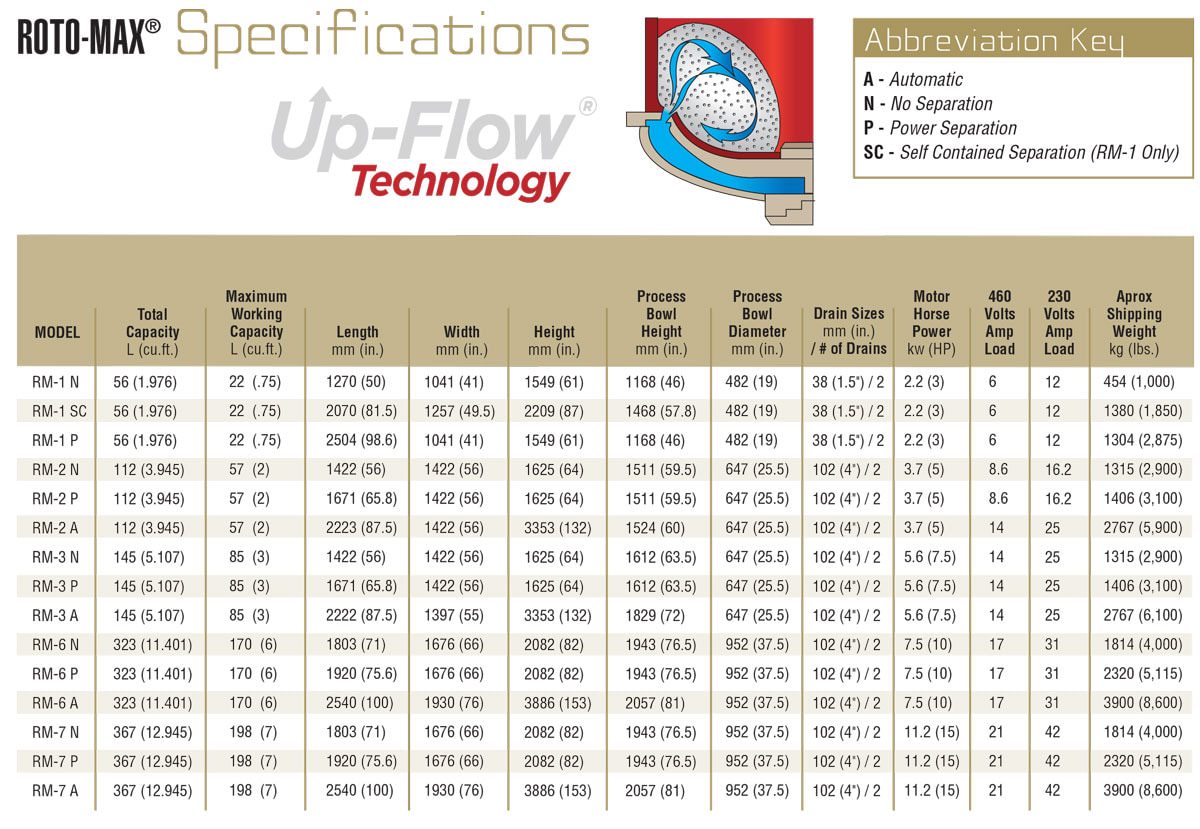
VERSA-FLOW SPIN-FINISH
The Versa-Flow Spin-Finish machine is a very high energy finishing system.
The machine uses a spinning tub of media that is either a very aggressive abrasive to remove heavy burrs from a work piece…or a very fine wet or dry polishing media for producing a very high color, or a low ra surface finish. Parts that are processed in the Spin-Finish are normally parts that: cannot have part-on-part contact; are high value parts; or where a lean manufacturing single part flow is needed.
The tub revolves at a range of speeds dictated by the need of aggression, the need of a more gentle action, or a light slurry. As the tub spins, it creates centrifugal energy and surface feet. The combination of the two create a dramatic combination of forces on the surface of the work-piece which is very effective in removing burrs and producing very low Ra surfaces. The centrifugal force produced by the spinning tub and weight of the media provides a form fitting abrasive mass moving around the work-piece.
How Versa-Flow Spin-Finish Operates:
- Parts are fixed using collets or special tooling on the spindle.
- Rotating spindle tilts parts into rotating mass/slurry.
- Part presentation to the mass is critical.
- Once process is complete, the part tilts out of the tub.
- Versa-Flow Spin-Finish is very well suited for several industries:– Aerospace
– Automotive
– Firearm
– Tool & Die
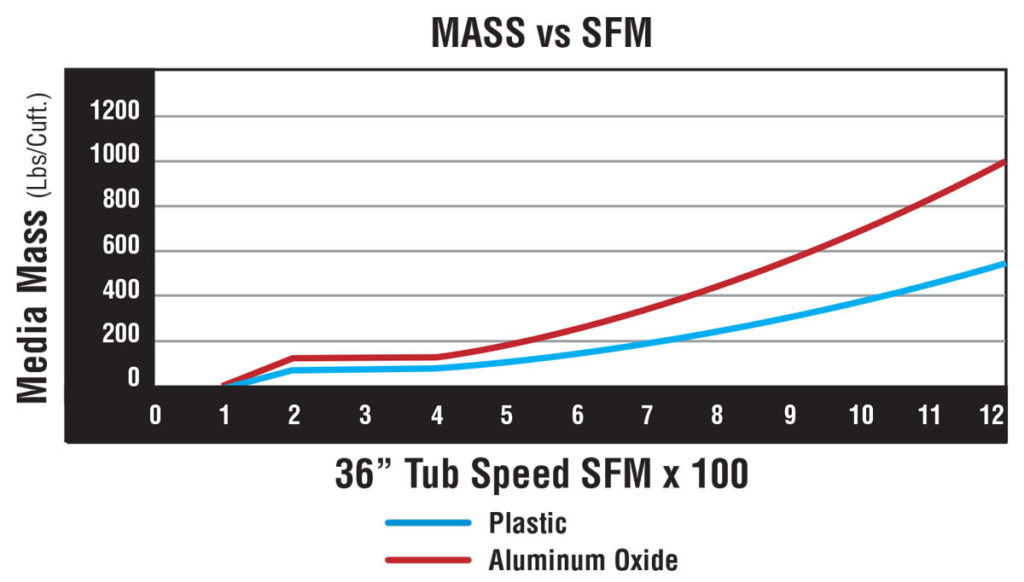
This is a very small sample of where Versa-Flow Spin-Finish can be used for solving finishing problems.